Client - Sanofi
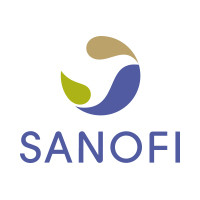
BSSEC were commissioned by Sanofi, global pharmaceutical manufacturing company, in order to assist with ESOS compliance and submission as Lead Assessor.
Client Requirements
Sanofi S.A. is a French multinational pharmaceutical company headquartered in Gentilly, France, the world’s fifth-largest by prescription sales. Sanofi engages in the research and development, manufacturing and marketing of pharmaceutical drugs principally in the prescription market, but the firm also develops over-the-counter medication. Sanofi has an annual turnover of approximately €33.8billion and 110,000 employees.
Building, process and transports energy audits were to be undertaken by BSSEC for Sanofi, ensuring all audit activity was compliant with ESOS. As Lead Assessor, BSSEC were to also maintain an ESOS evidence pack to substantiate and support the audits undertaken, and their findings and recommendations.
The buildings types at Sanofi requested for audit by BSSEC included production, offices, training, laboratories, storage and warehousing. A transport audit was also to be undertaken as initial energy analysis indicated that energy use exceeded 10% of total consumption.
Methodology
BSSEC delivered Lead Assessor duties, energy audits and other supporting activities in order to provide clients with an end-to-end compliance service. All duties and audits were undertaken in accordance with BS EN 16247 methodology.
Individual site energy audits were conducted, covering all areas of significant energy use including process, heating and hot water, lighting, small power, ventilation, cooling and catering. The transport audit and report were also included in this, where BSSEC reviewed the current state of energy use and emissions from business vehicle use.
The main purpose of the transport audit was to provide:
- A statement detailing the current energy consumption from the use of vehicles on business
- A review of the current vehicle management practices
- An identification of opportunities to increase efficiency and reduce both costs and its impact on the environment.
- Data, documents and interviews informed the transport audit.
Outcomes
Equipment was the biggest cost at industrial sites and production the biggest user. Based on the results and analysis of the audits, the following technical measures for industrial sites were some examined by BSSEC:
- Plant down-time
- Energy Policy
- Metering, Monitoring and Targeting
- LED lighting (internal and external)
- Fabric upgrades
- Solar PV array
- Install economisers to steam boilers
- CHP
- Repair of steam leaks
- Heat recovery and use
- Variable speed drives
- PIR Controllers
- Replacement of HVAC equipment
The key findings from transport auditing illustrated opportunities such as enhancements to the company car scheme to reduce emissions, the introduction of a formal fuel management programme and introducing a process to measure and reduce vehicle mileage.
As Lead Assessor, BSSEC then followed on to produce and sign off the ESOS pack for submission, including all associated evidence from throughout the auditing process.
“The environment we live in directly affects our health; at Sanofi, we are committed to monitoring our environmental footprint. In 2016, we reduced our CO2 emissions by 19.4% compared to 2010.”
Sanofi – Preserving the Environment Corporate Responsibility